https://arstechnica.com/?p=1646425
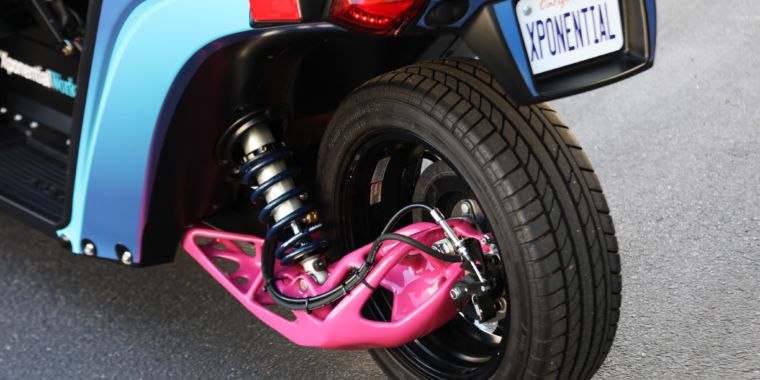
-
Arcimoto’s FUV is small, light, and nimble, but even with such a small vehicle there’s still the opportunity to save weight.
XponentialWorks
-
The AI-designed, 3D-printed rear swing arm weighs 34 percent less than the conventional part it replaces.
XponentialWorks
-
The brake pedal is 49-percent lighter.
XponentialWorks
-
This upper control arm is 52-percent lighter.
XponentialWorks
-
A screenshot from the design software. The green bit is the AI-generated design, the pink shape is the part it replaces.
-
Another screenshot showing the loads on the part.
accurately calls its electric three-wheeler a Fun Utility Vehicle—
four years ago, and it remains
one of the more entertaining vehicles
I’ve driven for Ars.
The company started delivering
the first FUVs to customers last September, but it’s not quite done with the design for this engaging little machine. As you probably know, weight is the enemy of efficiency, and even little EVs like this one have to carry around a hefty battery pack, in this case a 12kWh unit with 102.5 miles (165km) of city range. On Tuesday, Arcimoto and XponentialWorks announced they’ve been working together on a project that should make future FUVs even more efficient, thanks to lightweight suspension parts created using AI generative design and 3D printing.
“Our mission to rightsize the footprint of daily mobility means a continued commitment to optimizing not just the vehicle platform architecture, but all of its constituent parts as well. The speed at which the XponentialWorks team has made meaningful weight improvements to core components of the Fun Utility Vehicle is truly impressive,” said Arcimoto CEO Mark Frohnmayer in a statement.
XponentialWorks used ParaMatters’ AI software
for components like the FUV’s brake pedal, upper control arm, rear swing arm, and knuckle.
As with other AI-generated auto parts
, the results look far more organic than anything you’d expect to find on a road vehicle, and the weight savings is real–between 34 and 52 percent compared to the conventionally designed and constructed bits fitted to the versions we’ve tested in the past. It all happened pretty rapidly, according to XponentialWorks founder Avi Reichental.
“It took us about four weeks from taking a stock car to presenting a fully functional lightweighted FUV. With our unique capabilities to combine generative, additive and simulation technologies, we expect to be in production within the next six months,” he told Ars. For that to happen, everyone needs to be sure that the AI-designed, 3D-printed components are sufficient for the loads and stresses of life on the streets. “We believe that with our algorithmic finite element analysis solvers and powerful simulation technology, we can substantially compress the testing cycle and enhance the quality predictability and performance of each part,” Reichental told me.
Listing image by XponentialWorks
via Ars Technica https://arstechnica.com
January 21, 2020 at 08:07AM